CNH investeerde fors in Zedelgem
CNH investeerde fors in het New Holland Harvesting Center of Excellence in Zedelgem. De nieuwe CR 11- maaidorser van New Holland is dé enorme stimulans voor deze investering van 150 miljoen euro.
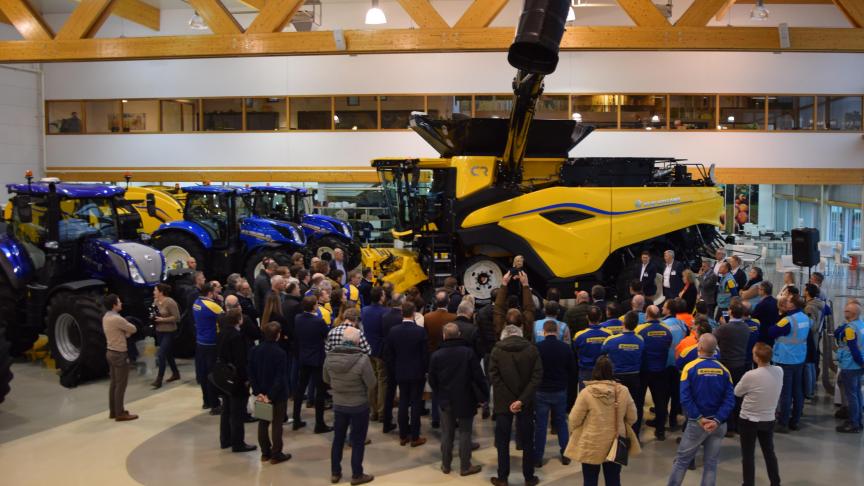
De laatste fase van zijn vijfjarige investeringsplan voor de R&D-productiefaciliteit in Zedelgem is ingezet. De investering is vooral bestemd voor de verdere ontwikkeling en productie van de nieuwe CR 11-maaidorser van New Holland. Dit is hun nieuwe topmodel dat eind 2023 op de Duitse landbouwmechanisatiebeurs Agritechnica in Hannover als enige een gouden innovatiemedaille kreeg (zie ook Landbouwleven van 14 december 2023).
Flexibeler en sneller
De investering zorgt voor een verbetering en aanpassing van de assemblagelijn. Daardoor moet meer flexibiliteit en productiesnelheid bekomen worden. Het logistieke gebied rond de assemblagelijn werd gerenoveerd en uitgebreid. De CR11 bevat immers zo’n 7.000 nieuwe onderdelen, of 95% van de gebruikte componenten.
De productielijnen voor zowel de CX- als CR-maaidorserseries komen nu samen én kennen een U-vormige opstelling. “Voor iedere 4 werkposten is een controlepunt opgenomen in de productieketting. Zo worden fouten in de productie snel opgespoord én is de machine niet te ver weg van het montagestation om aanpassingen te doen”, aldus fabrieksmanager Stefaan Van de Walle.
Een welkome vernieuwing in de productielijn is de komst van draadloze automatische voertuiggeleidingssystemen. Dit zijn een soort van robotjes die de in opbouw zijnde maaidorser dragen en van werkstation naar werkstation brengen. Deze zijn geschikt voor verschillende modellen. Dat maakt ook dat diversere maaidorserseries door elkaar gebouwd kunnen worden op de assemblagelijn. Deze verbetering, waarbij afgestapt wordt van een traditionele montagelijn, verhoogt de flexibiliteit van de maaidorserproducent.
De montagelijn werd voorzien van een nieuw olievulstation om netter en duurzamer te werken. Daarnaast kwamen er nieuwe werktuigen/gereedschappen bij, waardoor het personeel meer ergonomisch en veiliger zware componenten kan opbouwen.
Innovatiesteun
CNH kreeg voor zijn investering steun van het Vlaams Agentschap Innoveren en Ondernemen (Vlaio) van de Vlaamse overheid. Zij pleiten sterk voor innovatieprojecten in de Vlaamse regio. Daar is de ontwikkeling van de CR 11-maaidorser een mooi voorbeeld van. Er werd immers jarenlang gewerkt aan de optimalisatie van componenten en processen, samen met diverse onderzoekspartners uit het Vlaamse innovatie-ecosysteem.
“De investeringen in de productielocatie én het feit dat de nieuwe CR11 in Zedelgem wordt gebouwd, hebben een aanzienlijke impact op de werkgelegenheid, kennisontwikkeling en op verdere investeringen in de regio”, klinkt het bij Vlaio. Viceminister-president van de Vlaamse regering en gewezen minister voor Werk, Economie, Sociale economie, Innovatie en Landbouw Hilde Crevits was aanwezig bij de officiële opening van de nieuwe productielijn midden januari. Zij gaf te kennen ‘innovatie’ te prijzen als drijvende kracht achter werkgelegenheid en concurrentievermogen. Verder waardeerde ze CNH als partner om innovatie bij de landbouwer te krijgen én als een van de grootste werkgevers in West-Vlaanderen.
Tom Verbaeten, Chief Supply Chain Officer en tevens voormalig fabrieksmanager van Zedelgem, dankte in zijn toelichting tijdens de officiële inhuldiging van de nieuwe montagelijn niet enkel Vlaio. Hij bedankte ook Voka, Flanders Make, KU Leuven, Universiteit Gent en Universiteit Antwerpen. Met deze universiteiten wordt regelmatig samengewerkt voor de productontwikkeling. Bij het ontwerp van de nieuwe CR11 gebeurde dit om simulaties te maken van het dors- en reinigingswerk, maar ook werd de verspreiding van de oogstresten gesimuleerd en werd met de universiteiten gewerkt aan de gewichtsreductie.
“Nieuw is echt nieuw”
Het feit dat in Zedelgem op 1 locatie zowel ontwikkeling met de daadwerkelijke productie wordt gecombineerd, noemt Tom Verbaeten een van de sleutelelementen tot het succes van de innovaties. Wat betreft de CR11 geeft hij aan dat “nieuw ook echt nieuw is en geen klassieke tweejaarlijkse productupdate. Er zitten 80 patenten in de nieuwe CR11.” Marc Bombera, vicepresident crop harvesting product engineering, treedt hem bij: “Enkel het motorvermogen verhogen is niet voldoende om de dorscapaciteit te laten toenemen.” Tevens wijst hij op het machinegewicht dat evenredig toeneemt met de dorscapaciteit. “Bij de nieuwe CR11 is er daarom enorm ingezet op gewichtsbesparing.”
Geert Nerinckx, Global Product Manager CR, geeft aan dat binnen de maaidorsermarkt de nieuwe CR11 behoort tot de ‘Class 9+’ -categorie. Dit is een categorie die hij in de toekomst enkel maar groter ziet worden. Hij merkt een trend naar grotere maaidorsers in alle wereldregio’s. Tegen 2031 is de verwachting dat een derde van de maaidorsermarkt wordt ingenomen door dit type.
Als sterke punten van hun nieuwe dorser haalt hij aan dat de operationele kosten 15% lager liggen en dat er 25% tijd bespaard wordt tijdens het oogstseizoen. Hiernaast is er 20 % brandstofbesparing en daalt ook de CO2-emissie. “Dergelijke cijfers haal je niet met een productupdate, maar enkel door nieuwe innovatie.” De dorscapaciteit nam met 30% toe door langere en grotere dorsrotoren. De reinigingscapaciteit nam met 50 % toe door een dubbele reinigingsunit toe te passen en door de toegenomen verhoogde reinigingsoppervlakte.
Gouden innovatiemedaille
Geert Nerinckx: “Dé uitdaging was om binnen dezelfde maaidorsergabarit de productiviteit te verhogen met nieuwe technologie. De machine kan immers niet verbreden of verhogen omwille van wettelijke transportafmetingen. Omwille van deze innovatie hebben we in Duitsland een gouden medaille gewonnen. Daar zijn we als niet-Duits bedrijf bijzonder trots op.”
Hij wijst ook nog op het residumanagement van de CR11 of op de verspreiding van kaf en gehakseld stro. “Hoe egaal dit verdeeld is over de werkbreedte, bepaalt het succes van de teelt die volgt.” Frank Duquesne, Chief Engineering, pikt in op dit onderwerp. “Door de stofontwikkeling bij de stroverspreiding kan je het strooibeeld moeilijk visueel nagaan. Daarom hebben we een radarsysteem ontwikkeld om dit op te volgen.”
Verder wijst hij nog op de productontwikkeling die gebeurd is om gewicht en brandstof te besparen. De toerentallen van de motor en strohakselaar zijn teruggebracht om diesel te sparen. Een ander ontwerp van onderdelen zorgt ervoor dat ze even functioneel zijn, maar lichter qua gewicht. Ook buiten klassieke patronen denken hielp bij de gewichtsbesparing. Zo wordt de linker dorsrotor gebruikt om de aandrijving van de motor over te brengen op het invoerkanaal. Zo wordt bespaard op aandrijfonderdelen en dus op gewicht.
De motor in zijn lengterichting monteren en aansluiten op een cvt-transmissie hielp verder besparen op haakse overbrengingen en aandrijfonderdelen. Uiteraard draagt dit bij aan het verlagen van het totale machinegewicht.